The Art and Science of Curing Burley Tobacco
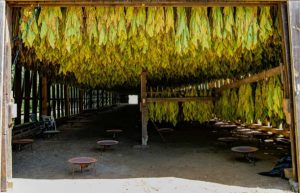
A Glimpse into History
In the mists of 1864, George Webb and Joseph Fore, on the fertile lands of Captain Frederick Kautz’s farm near Higginsport, Ohio, planted the seeds from Bracken County, Kentucky. These seeds would sprout into what we now recognize as Burley tobacco, embarking on a journey that would see Cincinnati crowned as its commercial heart by 1883, with its roots spreading through central Kentucky and Middle Tennessee.
The Quintessence of Burley Tobacco
Spanning continents, from the rolling fields of the United States to the lush landscapes of Brazil, Malawi, and Argentina, Burley tobacco unfurls its leaves, rich with a distinctive flavor, an enchanting aroma, and a robust nicotine content, setting itself apart in the pantheon of tobacco varieties.
The Ritual of Harvest
Harvesting Burley tobacco, akin to the methodical dance of flue-cured tobacco’s gathering, is performed with the priming technique, ensuring each leaf’s potential is meticulously unlocked.
The Essence of Air-Curing
In the serene embrace of well-aerated barns, the leaves of Burley tobacco embark on a transformative slumber. Suspended in time, they are caressed by the whispers of air for a duration that stretches from four to eight weeks, gradually shedding their moisture to don the golden-brown hue of maturity.
Optimizing the Air-Curing Ambiance
The alchemy of air-curing thrives under the vigilant gaze of temperatures cradled between 18.F and 32.F, with the air’s breath maintaining a humidity of 65 to 70%, crafting an ideal sanctuary for the leaves’ metamorphosis.
Navigating the Challenges of Timing
The capricious whims of nature often conspire to delay the planting and harvesting of Burley tobacco, ushering in a suite of challenges that test the resilience and adaptability of the curing process, demanding innovation and patience in equal measure.
The Symphony of Transformation
As leaves transition from their verdant youth, a myriad of physical and chemical ballets unfold, transmuting them into the aromatic, low-moisture treasures sought by aficionados, a testament to the curing process’s intricate complexity.
The Influence of Climate Inside the Curing Sanctuary
The soul of Burley’s quality is delicately molded by the interplay of moisture and temperature within the sacred confines of the curing barn. Here, a steady humidity, hovering in the realm of 72-75%, whispers the secrets of optimum transformation.
Historical Backdrop of Burley Tobacco
In the annals of tobacco cultivation, 1864 marks the year when George Webb and Joseph Fore sowed the seeds of what would become Burley tobacco on Captain Frederick Kautz’s farm in Ohio, seeds that hailed from Kentucky. By the year 1883, Cincinnati had emerged as the hub for this tobacco, signaling its proliferation across Kentucky and Tennessee.
The Stature of Burley Tobacco
Spanning continents, Burley tobacco is cultivated in prominent quantities in the United States, Brazil, Malawi, and Argentina. Esteemed for its robust flavor, enchanting aroma, and elevated nicotine levels, it holds a revered place in the tobacco domain.
Gathering of Burley Tobacco
Employing the priming method, akin to that used for flue-cured tobacco, the harvesting of Burley tobacco is a meticulous endeavor.
Air-Curing: The Essence of Burley Tobacco
At the heart of Burley tobacco’s uniqueness lies air-curing, a method where leaves are suspended in well-aerated barns, embarking on a drying journey spanning four to eight weeks.
Quintessential Conditions for Air-Curing
The art of curing Burley tobacco flourishes under temperatures oscillating between 18.F and 32.F, with the air’s humidity cradled in the 65% to 70% embrace.
Conundrums in Air-Curing
Alterations in planting and harvesting schedules often propel the crop towards a curing timeline later than the norm, ushering in a suite of curing challenges.
Chemical and Physical Metamorphoses
Curing is the alchemy that transmutes the Burley tobacco from its nascent yellowish-green, moisture-laden state at harvest to the aromatic, brown, and dry leaf, ready for the market.
The Influence of Temperature and Humidity
The essence of Burley’s quality is sculpted by the moisture and temperature ballet within the curing abode, with a rhythm dictated by an average daily humidity in the 72-75% range.
Probing Further into Burley Tobacco’s Realm
Environmental Tribulations
Temperatures dipping below 50.F in the curing inception fortnight may cast a greenish hue over the cured leaf, a deviation from the desired palette.
Technological Hurdles and Leaps
The year’s bounty, brimming with large, moist leaves, demands expansive spaces for curing, a challenge that technological strides and innovative farming practices are progressively addressing.
Technological advancements have unfurled new horizons for tobacco cultivators, enabling them to amplify yields and refine the quality of the cured tobacco. Low-profile structures, married with adept curing management, have been shown to yield a Burley that boasts a darker and more vibrant hue than its counterparts cured in traditional barns.
Deciphering Burley Tobacco
Burley tobacco, a light, air-cured variant primarily destined for cigarette crafting, boasts a significant production in an eight-state belt within the United States, notably Kentucky and Tennessee, alongside international grounds such as Brazil, Malawi, and Argentina. A genetic kin of the Virginia tobacco plant, the Burley variant necessitates a more delicate cultivation touch, thriving within more constrained geographies.
Distinguishing itself from other tobacco types like Virginia tobacco, Burley undergoes an air-curing process stretching from three to twelve weeks, culminating in a leaf that ranges from a light tan to a reddish-brown. This process imbues Burley with a bolder character, a dry texture accentuated with subtle cocoa nuances, and a medium to full-bodied flavor profile post-processing.
Burley’s prowess in flavor absorption makes it a cherished component in aromatic blends, attributing to it a slow-burning, cool-smoke quality that complements faster-burning, stronger blends.
The Curing Conundrum for Burley Tobacco Farmers
Amidst the serenity of tobacco fields, Burley cultivators grapple with challenges to maintain the idyllic curing conditions, weather whimsies, and the economic heft of the curing process. Fluctuating weather patterns, moisture-laden years leading to barn rot, and the stringent temperature and humidity requisites during curing weave a tapestry of hurdles that test the resilience and ingenuity of the farmers.
The Chronology of Curing
The transformational journey of Burley tobacco, from harvest to a market-ready state, unfolds over four to eight weeks of diligent air-curing. This period is a testament to the interplay of environmental conditions and the farmer’s adeptness in navigating these to achieve the quintessential Burley tobacco.
Concluding Insights on Burley Tobacco’s Curing Odyssey
At the heart of Burley tobacco’s journey from seed to smoke lies the intricate and pivotal phase of curing. This process, though fraught with hurdles, has seen a transformation through technological strides and refined methodologies, ensuring Burley tobacco’s esteemed status in the tobacco realm persists.
Deciphering the Numbers: A Glimpse into Burley Tobacco’s Curing Landscape
Production Narratives
In the year 2012, a visionary farm nestled near Danville, Va., in N.C., embarked on cultivating 15 acres of Burley amidst a larger expanse of 65 acres dedicated to flue-cured tobacco, illustrating the diverse agricultural tapestry of the region.
Efficiency in Curing: A Statistical Overview
The cultivation of Burley tobacco emerges as a testament to labor dedication, with stripping alone devouring around 73 worker-hours per acre, representing a significant chunk of the overall labor investment.
Demystifying Burley Tobacco Curing: A Curated FAQ Section
- Embarking on the curing journey: What does it entail for Burley tobacco?
- Impact analysis: How does curing sculpt the quality of Burley tobacco?
- Optimal conditions unveiled: What does the ideal curing environment look like?
- Environmental influence: The role of temperature and humidity in curing dynamics.
- Timing the transformation: The duration of the curing process explored.
- Diverse methodologies: An exploration of tobacco curing techniques.
- Distinctive paths: How Burley tobacco’s curing diverges from other types.
- Efficiency factors: What influences the success of the curing process?
- Labor intensity dissected: Understanding the efforts behind Burley tobacco curing.
- Innovative horizons: Strategies aimed at curing efficiency enhancement.
- Flavor and aroma: The influence of curing on Burley tobacco’s sensory profiles.
- Confronting challenges: Navigating the hurdles in the curing process.
- Nicotine nuances: The effect of curing on Burley tobacco’s nicotine levels.
- Common complications: Addressing issues encountered during curing.
- Evolutionary perspectives: Tracing the advancements in curing practices over time.
Enrich Your Knowledge: Essential Reads on Burley Tobacco Curing
- “Curing Burley Tobacco, 1991” – A definitive guide through the curing maze.
- “Harvesting and Curing Burley Tobacco, 1979” – Insights into the prelude and process of curing.
Discover More: Key Resources on Burley Tobacco Curing
- University of Kentucky, College of Agriculture – A deep dive into curing technologies .
- Total Leaf Supply – Unraveling flue-cured tobacco secrets .
- Burley Tobacco Extension – Addressing curing challenges .
- British American Tobacco – Exploring afforestation initiatives .
- Japan Tobacco Inc., Leaf Tobacco Research Lab – Chemical composition changes during curing .
- University of Georgia – A comprehensive guide to tobacco curing .
Academic Citations: Delving Deeper into Burley Tobacco Curing
- A journey from green to brown: The science of curing Burley tobacco https://burleytobaccoextension.ca.uky.edu/files/aeu-93_burley_curing_technology.pdf.
- The art of air-curing: Transforming Burley leaves in ventilated barns https://www.pmi.com/glossary-section/glossary/tobacco-curing.
- The labor of love: Stripping’s significant demand in Burley tobacco production https://meridian.allenpress.com/tobacco-science/article/doi/10.3381/12-023.1/131215/LABOR-PRODUCTIVITY-WITH-VARIOUS-INNOVATIONS-FOR.